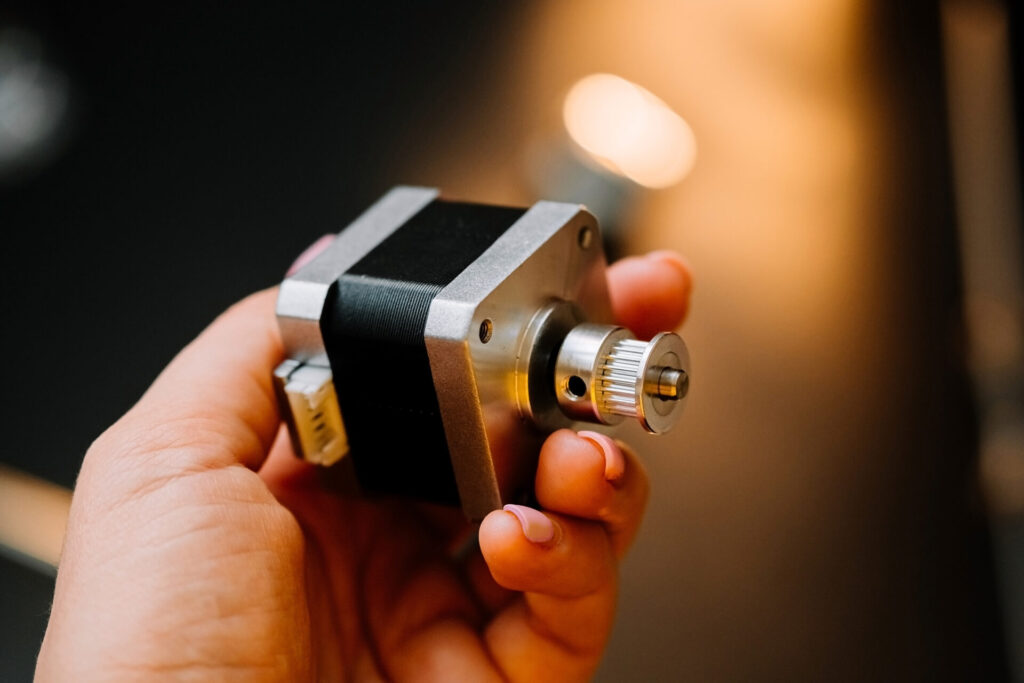
Points of interest in the research and development stage:
- Motor Type
- Detent Torque
- Holding Torque
- Current at Holding Torque
- Resistance
- Inductance
- Load Torque at Application Speed
- Noise at Application Speed
- Motor Life Expectancy
- Mechanical Requirements
Execution
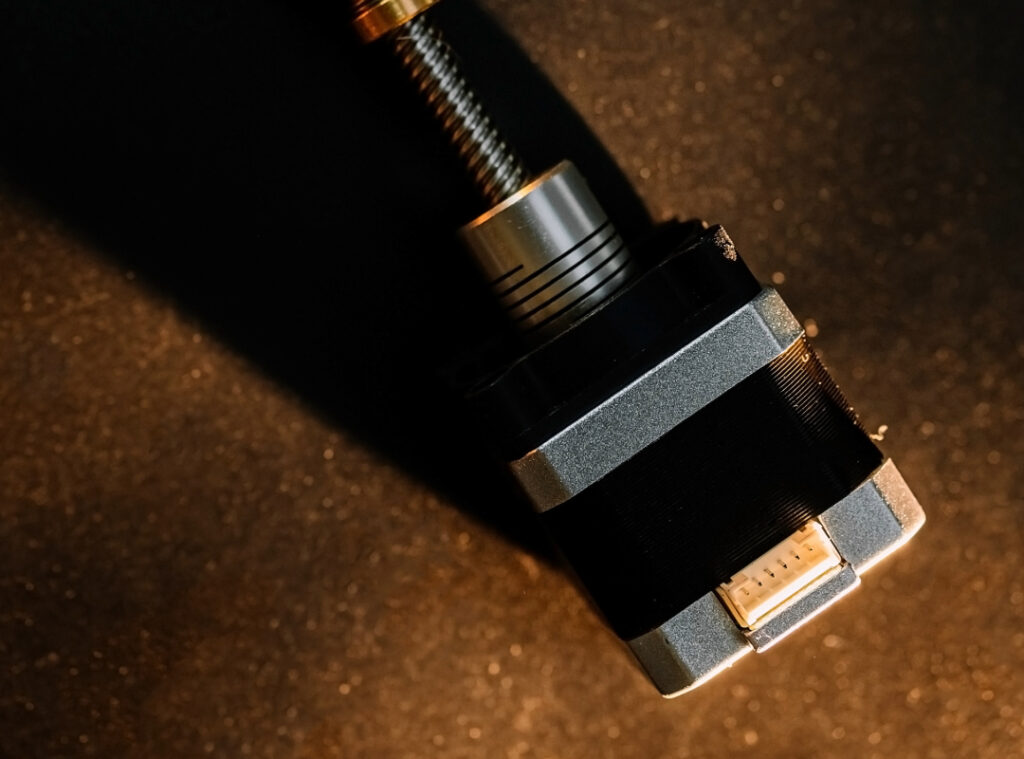
Start your project Now
Ready to get started? Hankscraft will be with you every step of the way as an invaluable partner, supplier, vendor, and extension of your team.
Contact us to learn more and to start your project.
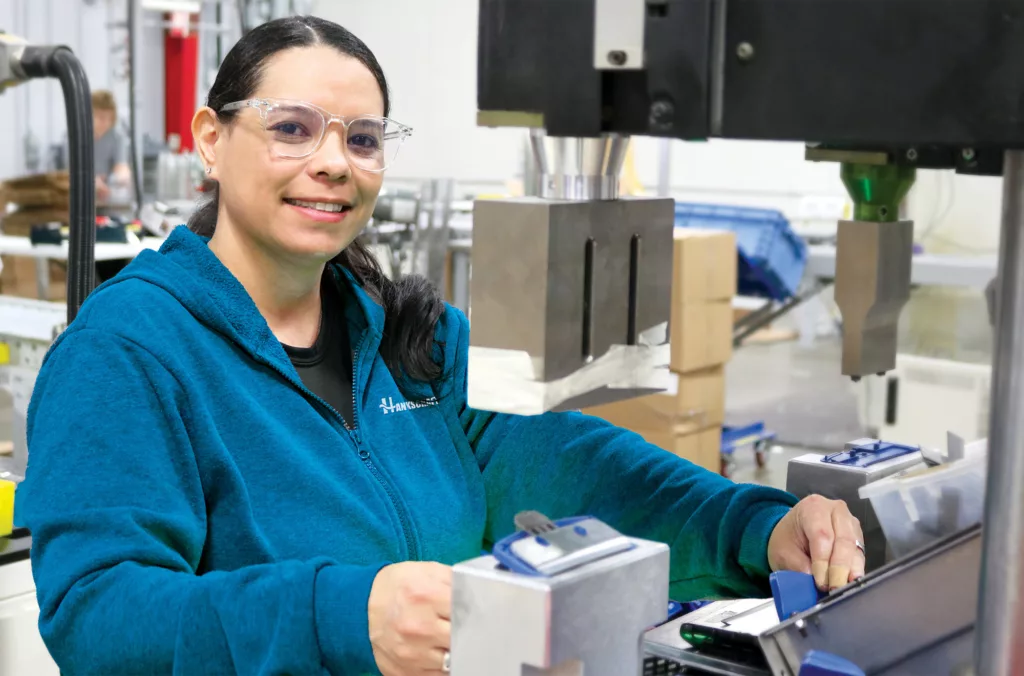